For automatic polishing of test pieces and image analysis of shperoidal grashphite
NAP-01
NAP-01 automatically tells you the nodularity of your cast iron melt within 5 to 6 minutes after receiving a test piece cast by pouring your melt in a proprietary shell mold cup.
Features of NAP-01
In-line installation
Because of its dry system, NAP-01 can be installed in a production line. Because of its automatic system, personal bias is avoided both in the polishing step and the structural analysis step. Further, analysis result is obtained within a few minutes and hence, can be immediately fed back to the melting operation.
Full automatic operation
All the processes from polishing to nodularity determination are done automatically, except the initial test piece casting.
In-line determination
Nodularity can be determined within 6 minutes at the minimum, and hence, quality judgment is done while the product is still in the production line.
Comparison with the conventional method
NAP-02 | NAP-01 | worker | |
---|---|---|---|
Time for judgment | 6 minutes | 6 minutes | about one day |
TP processing before polishing | Automatic cutting | Cutting is necessary | Company standard |
TP processing method | dry | - | dry / wet |
Polishing | dry | wet |
|
Installation | in-line | laboratory | |
Polish quality | complete polish for imaging | operator dependent | |
Data source | averaged from 5 views for one TP | operator dependent | |
Record | data is stored | test piece is stored | |
Personal bias | none | unavoidable |
Possible big cost cut
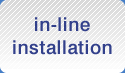
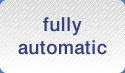
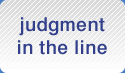

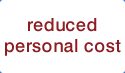
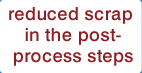
On each process step
TP automatic cutting
automatic polishing
Dry
I was not possible in conventional wet, can be installed in the field.
Quick polishing
The dry process, in stead of the conventional wet process, enabled in-line installation.
Reliable polish quality
Polishing quality is high and the time is quick (5 minute - ), making in-line judgment of the product possible.
![]() |
![]() |
![]() |
Cross section test piece was polished. | Analysis precision is improved by using the special consumables |
Multiple TP’s can be set by option. |
Automation
Does not require polishing by workers.
Unnecessary work polishing workers.There is no injury or damage caused by polishing.Improve the safety of the work environment. There is no need to place a worker polishing.
No personal bias
Heterogeneity of the speculum is eliminated by automation.
Customization of the polishing process can be
Setting of the polishing process can be 98Ch.
Polishing time can be set
You can set the minimum 5 minutes. If you set a long time, of course, to further improve the precision polishing.
Operation
![]() |
![]() |
Built-in liquid crystal display |
[Settings] Rotational speed polishing and polishing time Pressure and polishing polishing rate |
Safety measures
![]() |
![]() |
Safety cover | Openable cover |
Automatic imaging
Optical analogue type
Imaging corresponds to magnification of 100x
Digital image storage
Images can be stored.
Automatic nodularity determination
Ten views are automatically measured, where images can be selected if so desired. Determination is done without depending on the selection, and the fair and reliable result is expected without a need of worrying about personal bias.
No personal bias
Since the measurement set point, there is no difference between the results of human speculum.
Automatic analysis
Digital data storage
The analysis data can be stored.
The analysis data can be stored.
The averaged value from 10 views is displayed. A precise value is obtained, because analysis is made irrespective of the selection of views.
Because of the automatic system, operation time and results are person-independent.
analysis image
![]() |
![]() |
![]() |